Use Case Description
Background
The Haber process, a continuous chemical reaction, trades off yield maximization and energy efficiency. Through regulating parameters like temperature and pressure in the reaction between nitrogen and hydrogen over iron catalysts, ammonia production can be optimized. This process is highly energy-intensive, with ammonia synthesis accounting for 1.8% of global energy consumption. It's recognized as the largest carbon dioxide-emitting chemical process.
Problem
Process engineers are aware of production conditions that promote the forward reaction in the Haber process to maximize yield. This awareness will be in the form of experience as well as empirical historical data. Energy efficiency steps may be in place too but again these are typically implemented based on experience and historical trends.
Yield maximization is a critical aspect of the Haber process. The reaction is highly exothermic and reversible, and the ultimate yield of ammonia is influenced by various factors, including temperature, pressure, catalyst selection, and gas composition. Adapting these factors to maximize high yields under varying production conditions, is challenging to do in real-time.
While maximizing yield, process engineers also endeavor to maximize energy efficiency. Typically this is tackled by minimizing the cost of compressing feed gas by controlling for recycle and feed compressor ratios, operating conditions, etc. Additionally, engineers wish to reduce CO₂ emissions by minimizing the amount of methane burned to produce steam for the steam reforming reaction.
Maximize ammonia yield while minimizing energy consumption and CO₂ emissions.
Ammonia production is incredibly energy intensive, predominantly due to steam methane reforming. Improving the energy efficiency of ammonia production is critical to producers. Not least because ammonia, primarily used for fertilizer production today, is increasingly being seen as a zero-carbon fuel. This is because ammonia can act as a medium store and transport for chemical energy, as a transport fuel, and as a store for thermal energy.
The current approach to ammonia yield maximization can lead to:
- financial loss due to unnecessary usage of fuel, and
- environmental cost of incurring Scope 2 emissions due to unnecessary consumption of fuel.
Click here to download the entire Playbook
Fero Labs Solution
Ammonia producers can use Fero Labs software to ensure maximum yield of ammonia during the continuous Haber process while minimizing energy usage and CO₂ emissions. Fero can adapt to process restrictions such as minimum and maximum permitted temperatures and pressures in reactors, while adapting to variable production conditions.
A “Live Fero Analysis” for this use case presents two screens:
- Detailed View: for process engineers to monitor production and take action at any moment. Here, Fero recommends how yield can be maximized under current production conditions. Restrictions can be placed on the maximum allowed values for temperature and pressure, enabling engineers to safely explore energy minimization objectives while continuing to maximize yield.
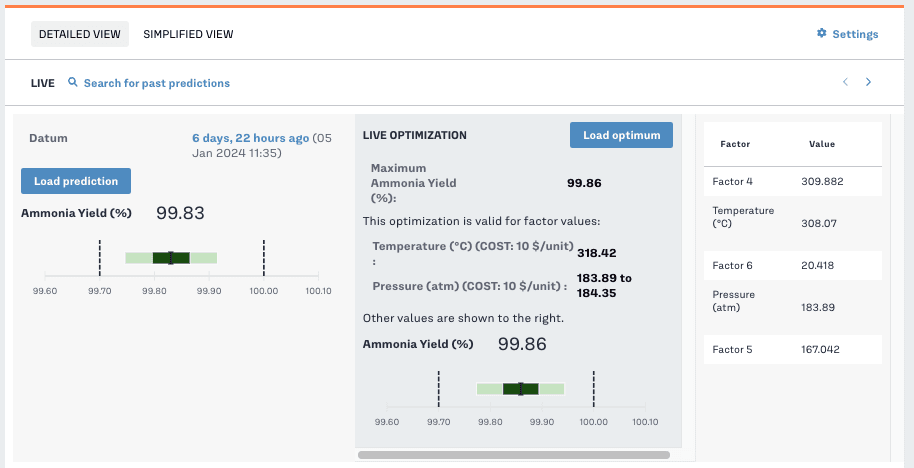
- Simplified View: for plant operators to know exactly what action to take to maximize yield and minimize energy consumption.

Process & Business Outcomes
Increased production line profitability
Maximizing ammonia yield makes the production line more profitable for two reasons: fewer reactants are wasted creating by-products and increased profit potential due to a higher volume of end product being produced.
Ammonia plants leveraging Fero across their operations can expect up to 1.5% yield improvement, providing top-line growth opportunity.
Tightened yield control and stability
With Fero Labs providing optimal recommendations for maximizing ammonia yield, the variability of process yield over time will be reduced, allowing for a more efficient and stable process.
With full adoption of Fero Labs on the production line, ammonia plant operators can see up to 10% reduction in yield variability.
Energy cost minimization
Ammonia plant operators seek to minimize the amount of energy consumed during production. Overly aggressive reduction campaigns deliver diminishing returns as the trade-off involves reduced yields. In turn, unnecessarily high temperatures accelerate catalyst deterioration and carry high costs.
With Fero deployed on an average-sized production line with average energy cost of $0.14/kWh, plant operators can easily surpass $1 million in savings per year.
Commensurate Scope 2 carbon minimization
Reducing energy consumption directly reduces the Scope 2 carbon footprint of ammonia production. Since Scope 2 accounts for about one-third of traditional ammonia production’s footprint, reducing energy consumption leads to a commensurate 3–4% reduction in Scope 2 emissions. Fero can provide reporting capabilities that directly track and account for this reduction.
Fero Labs Adoption Timeline
Plant teams can collaborate to set up and deploy Fero Labs. Below is a timeline highlighting typical steps. With Fero’s easy-to-use, no-code interface, this can be achieved in a matter of weeks, not months or years.
Data Requirements
Plant teams can collaborate to set up and deploy Fero. Below is a timeline highlighting typical steps. With Fero’s easy-to-use, no-code interface, this can be achieved in a matter of weeks, not months or years.
Activating This Use Case
Consider our Industrial Use Case Playbooks as inspiration and tactical ideas for your team to align on to maximize the efficiencies of your plant.
Each Playbook has a matching Use Case Blueprint which provides more detailed steps to activate each use case within the Fero Labs platform.
If you’re curious to see these in action please book a free feasibility study with our team!
Together, let us continue to push the boundaries of what's possible, driving towards a future where industrial manufacturing is not just efficient and sustainable but truly transformative in its impact on society and the world at large.
Thank you for joining us on this journey, and we look forward to continuing to partner with you in your pursuit of excellence.
Download the entire Ammonia Process Energy Minimization Playbook to access additional tables and details about this industrial use case.