Fero is designed to cut through the complexity of industrial data—no matter how peculiarly it's formatted. Our machine learning-powered software helps manufacturers cut costs while maximizing efficiency and minimizing emissions.
Here's a sampling of what you can do with Fero:
- Consume data sources as they exist, with easy connectors to standard industrial databases like OSI PI and IP21
- Merge different data sources in software without code
- Filter and transform data without code
- Configure processes based off your data sources in order to automate more complex transformations
- Get live recommendations
In this post, we'll look at how a top global steel manufacturer went through these steps to maximize cost savings, saving millions of dollars annually across its entire footprint.
Initially, engineers hoped to use Fero to lower production costs, without compromising the quality of the steel they produced. Their current analytical tools provided some cost-saving predictions, but fell short in terms of being able to make real-time adjustments or evaluate multiple nonlinear relationships between data points. They knew they weren't taking full advantage of all the data they were generating on the factory floor.
That's where Fero came in.
Engineers started working with Fero by taking static pulls from various process, lab, and quality related databases. Within Fero, they were able to easily merge these data sources together and filter them by the specific product and grade types that were relevant for analysis.
Once confident in Fero's high accuracy, they switched over to live mode to unlock maximum cost savings.
Without Fero, operators often erred on the side of adding too many costly raw ingredients in order to meet physical property specifications and avoid the even more costly mistake of a scrapped batch. But the live recommendations were a game changer. Delivered in under a minute, they told engineers exactly how much of each alloy they needed to add—minimizing waste, and maximizing savings.
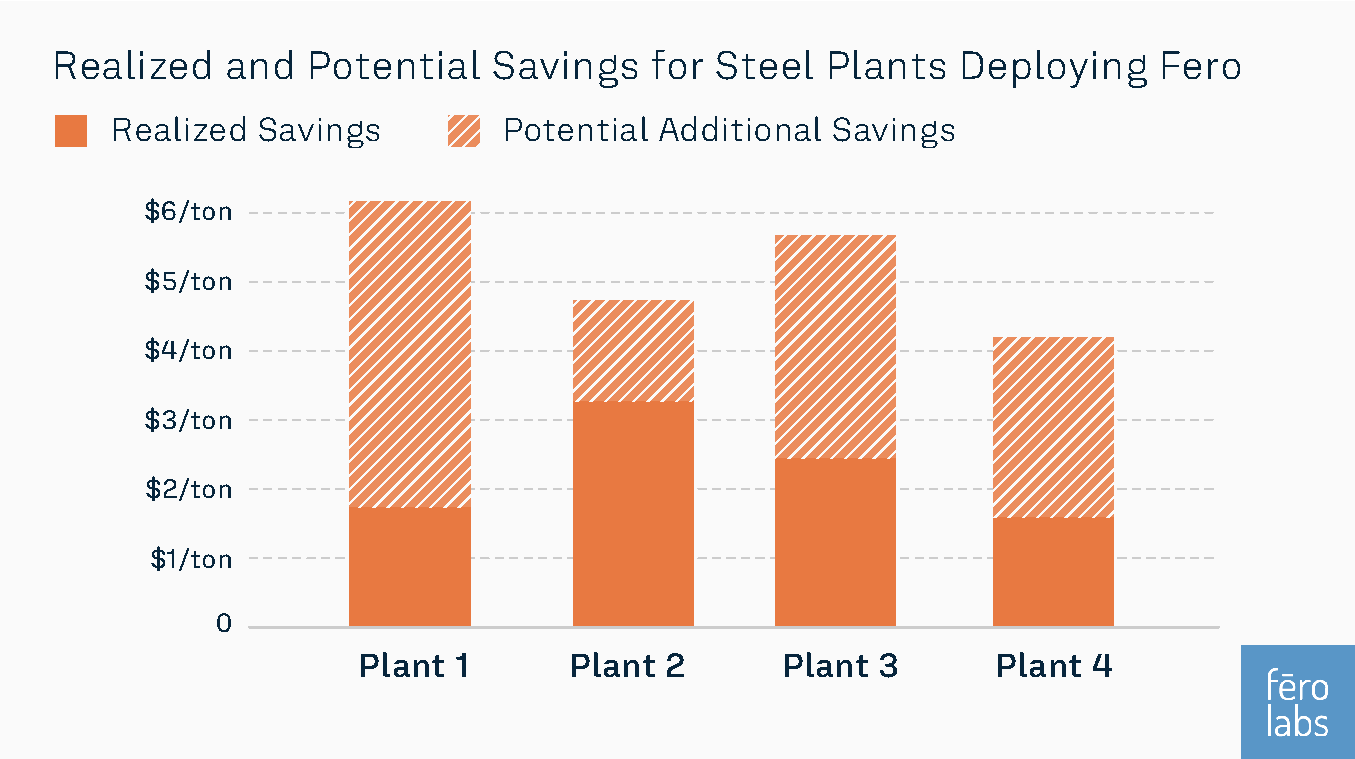
Within six months of deploying Fero, the average steel plant sees $1-$6 per ton in raw material savings. Scaled across use cases and plants, the results are even more dramatic.
This example illustrates how Fero gives users the ability to turn their industrial data into actionable analyses through its suite of data processing tools and machine learning. Similar stories exist across sectors, from cement to chemicals. With Fero, complex industrial data becomes a tool you can use to guide decision-making and maximize profits.