Use Case Description
Background
An electric arc furnace (EAF) in a steel plant is a type of furnace that uses electricity to heat and melt scrap metal to produce steel. EAFs are used in the steel industry for their flexibility and efficiency in recycling scrap metal. The process involves charging the furnace with scrap metal and applying an electric current to create an arc between the electrodes and the metal, which melts the metal to the desired temperature for casting.
Problem
One of the key goals in steelmaking is to ensure that mechanical properties are kept within specifications. This is hard to achieve since there is a large variability in the chemical composition of scrap that is used as input to the process.
To process each batch of scrap metal, various ferroalloys are added at the ladle furnace. These additions at the ladle furnace are critical to adapting to variable scrap chemistry and meeting product quality metrics. Process and quality engineers operating at EAF mills define static product recipes that aim to keep mechanical properties within specifications for a wide range of scrap variability. The challenge is compounded with rolling mill variability, cold-charge workflows, and annealing processes.
Examples of these ferroalloys are:
- Ferro-vanadium (FeV)
- Ferro-niobium (FeNb)
- Silico-manganese (SiMn)
Minimize ferroalloy additives while maintaining mechanical properties (tensile and yield strength) within specification.
The current solution to this problem is to develop static grade-books (e.g., in an Excel document) for the worst-case scenario. These frequently advocate using a larger amount of ferroalloys than is necessary, which results in:
- financial loss due to unnecessary usage of key alloys, combined with a higher risk of scrap/regrade, and
- environmental cost of incurring Scope 3 emissions due to the wasted raw materials.
Fero Labs Solution
Electric arc furnace operators can use Fero Labs software to minimize the addition of ferroalloys while ensuring that Tensile and Yield Strength KPIs are kept within product specifications. Worst-case rolling mill parameters can be used to minimize risk of product re-grades.
A Live Fero Analysis for this use case presents two screens:
- Detailed View: for production and quality engineers to monitor production and take action at any moment
Simplified View: for operators in ladle pulpits, with critical information clearly presented.
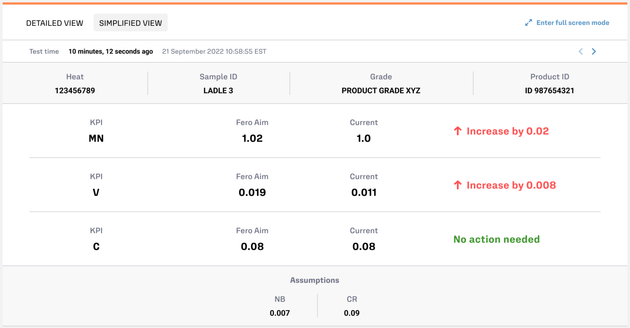
Process & Business Outcomes
Tightened variation of end-of-line mechanical properties
With Fero Labs providing optimal recommendations for ferroalloy additions at the ladle, scrap variability no longer translates to end-of-line mechanical property variation.
Since each batch is optimized to meet its specific quality metrics relative to its specific chemical composition at the ladle, Tensile and Yield Strength measurements become more stable.
With a full adoption of Fero Labs software on the production line, EAF mills can see up to 20% reduction in Tensile and Yield Strength variability, within production grades. Knowing that production will reliably meet its specifications leads to smoother operations.
Increased proportion of scrap in production
With high-grade steelmaking, it can be difficult to rely solely on scrap metal to hit specific chemistry targets and mechanical property specifications. Some EAF mills may blend scrap with direct steelmaking.
With Fero Labs optimizing each batch of scrap based on its chemical properties, EAF mills that blend scrap can expect up to a 25% increase in scrap metal usage in production.
Measurable cost savings from minimizing ferroalloy consumption
Static recipes for product grades lead operators to add unnecessary amounts of ferroalloys at the ladle. With Fero Labs optimizing for cost, while maintaining stability of end-of-line mechanical properties, operators can minimize what added ferroalloys.
With a full adoption of Fero on the production line, EAF mills can expect up to 2.8% cost savings in raw materials.
Commensurate Scope 3 carbon footprint minimization
The minimization of ferroalloys tackles the tricky problem of reducing Scope 3 emissions.
Since almost half of EAF steelmaking’s carbon footprint falls into Scope 3, a reduction here can reduce the carbon footprint of production by up to 15%. Fero Labs provides reporting capabilities that directly track and account for this reduction.
Fero Labs Adoption Timeline
EAF mills with specialized teams can collaborate to set up and deploy Fero. Below is a timeline highlighting typical steps. With Fero’s easy-to-use, no-code interface, this can be achieved in a matter of weeks, not months or years.
Data Requirements
Learn what data is required for this use case, and in which format it can be provided. From your laboratory to your melt shop or rolling mill if available, download the Playbook to access information on ideal data sources, formats, and time periods.
Activating This Use Case
Consider our Industrial Use Case Playbooks as inspiration and tactical ideas for your team to align on to maximize the efficiencies of your plant.
Each Playbook has a matching Use Case Blueprint which provides more detailed steps to activate each use case within the Fero Labs platform.
If you’re curious to see these in action please book a free feasibility study with our team!
Together, let us continue to push the boundaries of what's possible, driving towards a future where industrial manufacturing is not just efficient and sustainable but truly transformative in its impact on society and the world at large.
Thank you for joining us on this journey, and we look forward to continuing to partner with you in your pursuit of excellence.
Download the entire Ferroalloy Additive Minimization Use Case Playbook to access additional tables and details about this industrial use case.