Use Case Description
Background
Many large-scale chemical plants and refineries involve the operation of equipment that is often jacketed with flowing water to remove heat. For such types of equipment, induced draft cooling towers are often used to cool the recirculated water and regulate the temperature of the operating units. These cooling towers operate by evaporating parts of the hot water in cooler air facilitated by fans that circulate air within the tower.
Problem
The effectiveness of cooling and the rate of evaporation are controlled by several factors: the speed of the fans in the towers, the air temperature, humidity, and air flow rate. Additionally, to compensate for water drift loss due to evaporation, the system requires the addition of makeup water.
Optimizing the fan speeds of cooling towers is essential for reducing both energy and water consumption, while also ensuring precise control of equipment set-point temperatures across various heat loads and environmental conditions.
Typically, manual intervention is necessary to adjust the cooling tower fan settings to achieve a desirable temperature, which can be both time-consuming and labor-intensive, especially if the cooling tower operates with multiple fans and at various efficiencies. In most situations, process engineers operating a plant or refinery are not available to manually adjust the settings to simultaneously achieve the temperature set-point and minimize energy and water usage.
Minimize the cost of energy and water consumption while maintaining set-point temperatures of an induced draft cooling tower.
Process and control engineers can resort to integrating their cooling towers with a control system, such as a PID control, that automates fan tuning. However, in general, PID controls are typically configured to only achieve the desired set-point temperatures using a single input, without necessarily trying to operate the cooling tower efficiently.
Fero Labs Solution
Plant operators can employ Fero Labs to optimize the fan speeds and air flow rates of cooling towers, while ensuring that the necessary set-point temperatures are met and the cost of energy and water consumption is minimized. Fero’s real-time optimization solutions can determine the most efficient operational parameters. Moreover, once the optimal settings are identified, they can be directly communicated to a control system that automatically adjusts the control settings.
For control systems that incorporate temperature PID controllers, which are already integrated with the cooling tower fan speeds, a solution like Fero can be implemented to fine-tune the fan speed adjustments. Essentially, Fero can be configured to modify the fan speed offsets in relation to the initial fan speed settings determined by the PID controller. These adjustments are introduced as disturbances to the PID controller, providing an additional layer of control that allows for more precise management of cooling tower operations.
A “Live Fero Analysis” for this use case presents two screens:
- Detailed View: for plant operators to monitor cooling tower performance and take action at any moment. Here, Fero recommends how the cost of energy and water consumption can be minimized while the temperature is maintained. Restrictions can be placed on the maximum or minimum allowed values for water flow rates, enabling engineers to safely explore cost minimization objectives.

- Simplified View: for plant operators to know exactly what action to take to reduce energy and water consumption while maintaining the cooling tower outlet temperature.
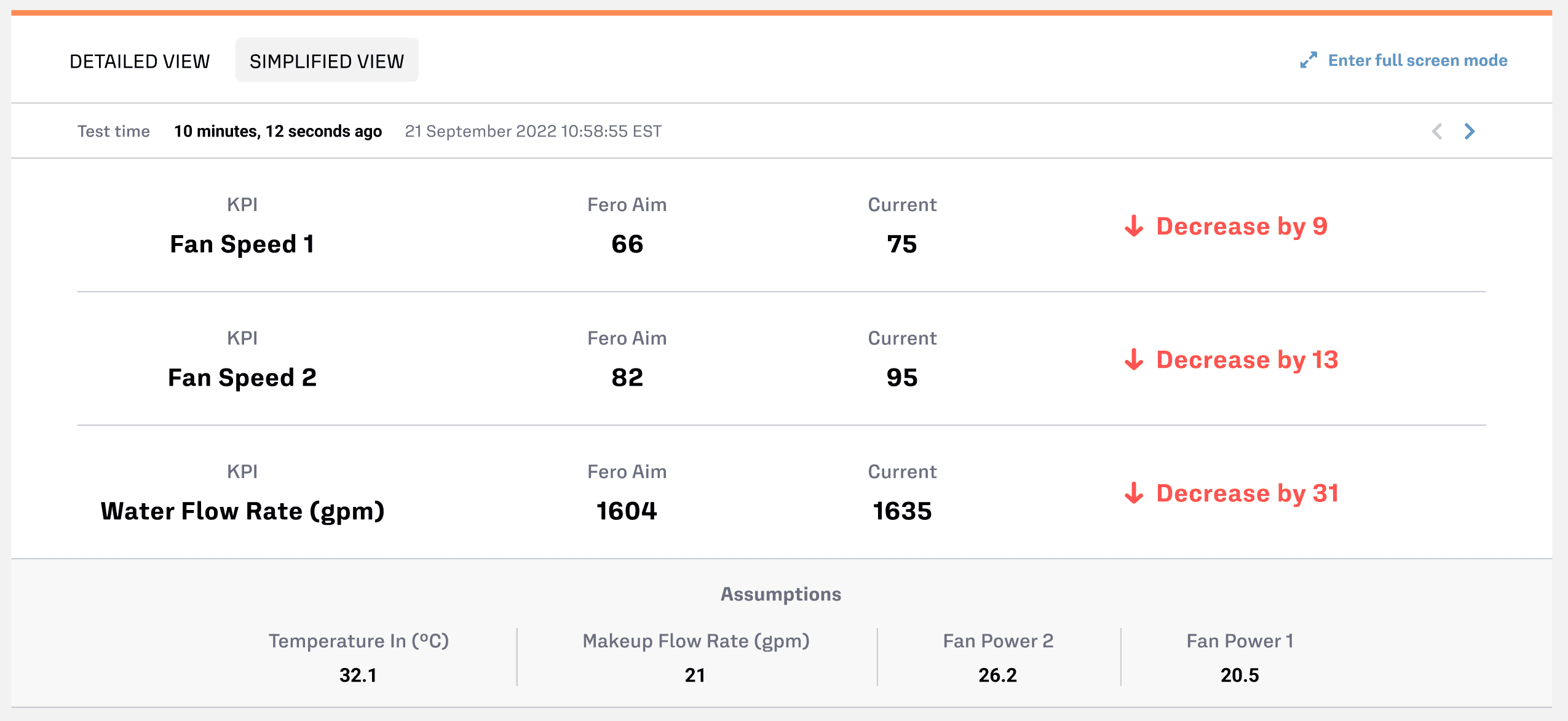
Process & Business Outcomes
Precise set-point control and stability
Fero providing optimal recommendations for fan speeds will ensure the cooling tower desired temperatures are achieved under various heat loads and environmental conditions without additional hardware. Moreover, Fero can act as a software layer on top of existing PID control systems allowing for more precise management of cooling tower operations.
Energy and water cost minimization
Fero’s optimizer enables cooling towers to minimize the cost associated with the energy and water consumed during production while ensuring that the desired set-point temperature is within a desired tolerance. This can reduce energy and water usage costs by up to 12% of nominal costs.
Commensurate Scope 2 carbon minimization
Reducing energy consumption directly reduces the Scope 2 carbon footprint of cooling towers. With full adoption of Fero, plant operators can also expect up to a commensurate 8% reduction in Scope 2 emissions. Fero can provide reporting capabilities that directly track and account for this reduction.
Fero Labs Adoption Timeline
Plant teams can collaborate to set up and deploy Fero Labs. Below is a timeline highlighting typical steps. With Fero’s easy-to-use, no-code interface, this can be achieved in a matter of weeks, not months or years.
Data Requirements
Plant teams can collaborate to set up and deploy Fero. Below is a timeline highlighting typical steps. With Fero’s easy-to-use, no-code interface, this can be achieved in a matter of weeks, not months or years.
Activating This Use Case
Consider our Industrial Use Case Playbooks as inspiration and tactical ideas for your team to align on to maximize the efficiencies of your plant.
Each Playbook has a matching Use Case Blueprint which provides more detailed steps to activate each use case within the Fero Labs platform.
If you’re curious to see these in action please book a free feasibility study with our team!
Together, let us continue to push the boundaries of what's possible, driving towards a future where industrial manufacturing is not just efficient and sustainable but truly transformative in its impact on society and the world at large.
Thank you for joining us on this journey, and we look forward to continuing to partner with you in your pursuit of excellence.
Download the entire Induced Draft Cooling Tower Energy and Water Minimization Playbook to access additional tables and details about this industrial use case.