Use Case Description
Background
The production of vinyl chloride monomer (VCM), used to synthesize poly-vinyl chloride (PVC) involves a continuous, multistep process: chlorination of ethylene to produce ethylene dichloride (EDC), oxychlorination of ethylene, EDC purification, EDC cracking, and VCM purification.
This last step is crucial as it ensures the quality and purity of VCM, determining its suitability for storage and subsequent polymerization into PVC in downstream processing. High purity levels are important for achieving desired properties in final PVC production.
Problem
The purity of VCM can vary based on a number of process conditions including EDC concentrations, reaction temperatures, distillation tower temperatures and heat duties, reflux ratios, and the degree of subcooling.
These fluctuations present a considerable challenge for plant operators in maintaining high VCM purity while avoiding unplanned maintenance on the production process. Moreover, operators are required to adhere to strict operational safety protocols due to the high flammability and toxicity of VCM, limiting the adjustments they can make to process parameters.
This constraint, coupled with a limited understanding of the root causes behind low production quality, complicates the task of determining appropriate strategies to drive the process and when to perform necessary maintenance.
Proactively intervene on process conditions by forecasting future values of the vinyl chloride monomer concentrations based on present variable operating conditions.
Failure to maintain high purity levels of VCM can lead to significant reductions in downstream PVC yields and increased operational costs associated with the removal of byproducts and unreacted VCM, prompting plant operators to adopt a conservative maintenance protocol including aggressively scheduled maintenance activities.
Such a strategy often results in frequent production stops, incurring substantial operational expenses. These costs could be minimized if control operators were able to make well-timed interventions before observing declines in VCM purity levels.
Fero Labs Solution
With Fero software, plant operators can closely monitor and forecast VCM purity during the purification process under various operating conditions.
More specifically, Fero pinpoints the key operating parameters affecting VCM purity based on root cause analysis and leverages machine learning-based forecasting methods to project future values of VCM purity, providing timely alerts for when interventions are needed to mitigate low purity levels.
This proactive approach ensures optimal production efficiency and maximizes production throughput for each operational campaign.
A “Live Fero Asset” for this use case presents the following interactive screen:
- Forecast view: in the top panel, plant managers and control engineers can monitor past VCM purity levels and observe forecasts, with the transition from historical to forecasted data marked by the solid black vertical line. Here, Fero projects how past and current operating conditions and VCM purity might evolve, highlighting potential decline in purity that may necessitate corrective action. To aid in decision-making, Fero provides forecasts surrounded by confidence intervals. Should there be a need for proactively adjustments to maintain VCM purity within specification, operators are guided to adjust the key operational parameters, such as distillation reboiler and condenser heat duties. In scenarios where such interventions are insufficient to restore VCM purity to acceptable levels, Fero’s forecasting model aids in strategic planning by suggesting a cost-effective maintenance schedule.
- Scenario view: in the bottom panel, plant operators can monitor the corresponding past operational parameters and observe their forecasts. This allows for the adjustment of forecasted values to assess their impact on projected VCM purity displayed in the top panel. This enables operators to simulate adjustments in operating parameters or set-point values based on anticipated changes. Moreover, this simulation capability supports the exploration of strategic operational adjustments that could reduce production halts due to purity levels falling out of specification.
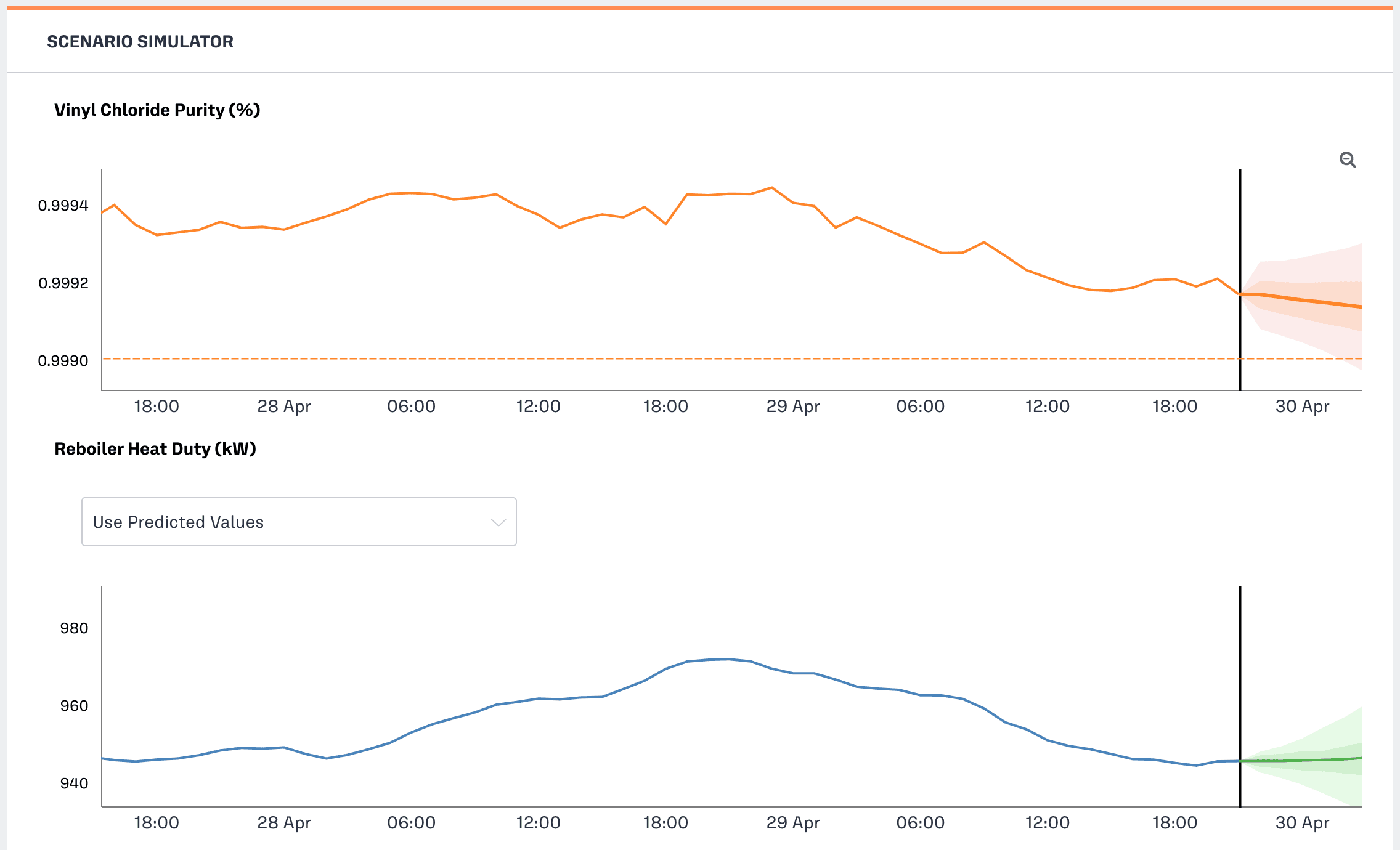
Process & Business Outcomes
Increased profitability by reducing out-of-spec VCM production
Soft sensors can enable control engineers to make necessary adjustments to operational conditions based on product quality forecasts. This can increase production throughput by up to 15%. In a market heavily limited by production capacity, this improvement could also translate into a top-line benefit of up to 15%.
Conduct “what-if” simulations to gauge the effects of process modifications
Fero Labs software application enables plant engineers to test hundreds of different “what-if” operating scenarios for future time horizons. This is particularly beneficial when operators possess insight into potential adjustments in operating parameters or setpoint values in the next 5 days and seek to understand their impact on the forecasted VCM purity. By enabling this level of predictive analysis, operators can identify effective strategies that not only improves production quality, but significantly enhances overall operational efficiency and minimizes downtime.
Informed decision-making to mitigate unplanned shutdowns
Plant operators can gain confidence in deciding when to initiate a shutdown or make an operational change when process abnormalities occur. In scenarios where interventions are insufficient to restore VCM purity to acceptable levels, Fero’s forecasting model aids in strategic planning by recommending cost-effective maintenance schedules.
With full adoption of Fero Labs software, plant operators can expect to experience up to 36% decrease in unplanned production shutdowns.
Fero Labs Adoption Timeline
Plant teams can collaborate to set up and deploy Fero Labs. Below is a timeline highlighting typical steps. With Fero’s easy-to-use, no-code interface, this can be achieved in a matter of weeks, not months or years.
Data Requirements
Plant teams can collaborate to set up and deploy Fero. Below is a timeline highlighting typical steps. With Fero’s easy-to-use, no-code interface, this can be achieved in a matter of weeks, not months or years.
Activating This Use Case
Consider our Industrial Use Case Playbooks as inspiration and tactical ideas for your team to align on to maximize the efficiencies of your plant.
Each Playbook has a matching Use Case Blueprint which provides more detailed steps to activate each use case within the Fero Labs platform.
If you’re curious to see these in action please book a free feasibility study with our team!
Together, let us continue to push the boundaries of what's possible, driving towards a future where industrial manufacturing is not just efficient and sustainable but truly transformative in its impact on society and the world at large.
Thank you for joining us on this journey, and we look forward to continuing to partner with you in your pursuit of excellence.
Download the entire Vinyl Chloride Monomer Purity Forecasting Playbook to access additional tables and details about this industrial use case.